Izgradnja dugih cjevovoda zahtijeva brojne zavarene spojeve pojedinih cijevi. Kvaliteta zavarivanja može imati značajan utjecaj na performanse cijelog autoceste. Metode kontrole zavarenih spojeva omogućuju da se s dovoljnom razinom pouzdanosti govori o njihovoj kvaliteti.
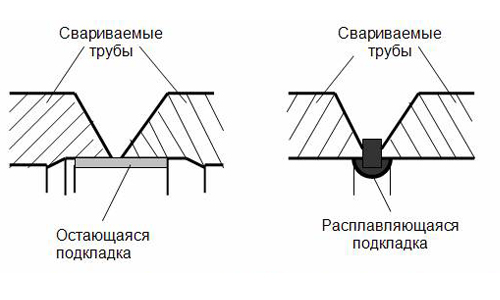
Shema montaže spojeva cijevi zavarivanjem.
Vladini standardi strogo reguliraju potrebu provjere pouzdanosti cjevovoda. Takva provjera je potrebna kako bi se osigurala sigurnost njihovih usluga. Ispitivanje bez razaranja zavarenih spojeva cijevi uključeno je u objektivni sustav kontrole kvalitete autocesta i obavezan je i učinkovit način procjene njihove pouzdanosti i sigurnosti.
Formiranje defekta
Pri provođenju zavarivanja cjevovoda i odgovarajućih toplinskih učinaka u zavarenom području i susjednim područjima mogu se pojaviti defekti (lom).
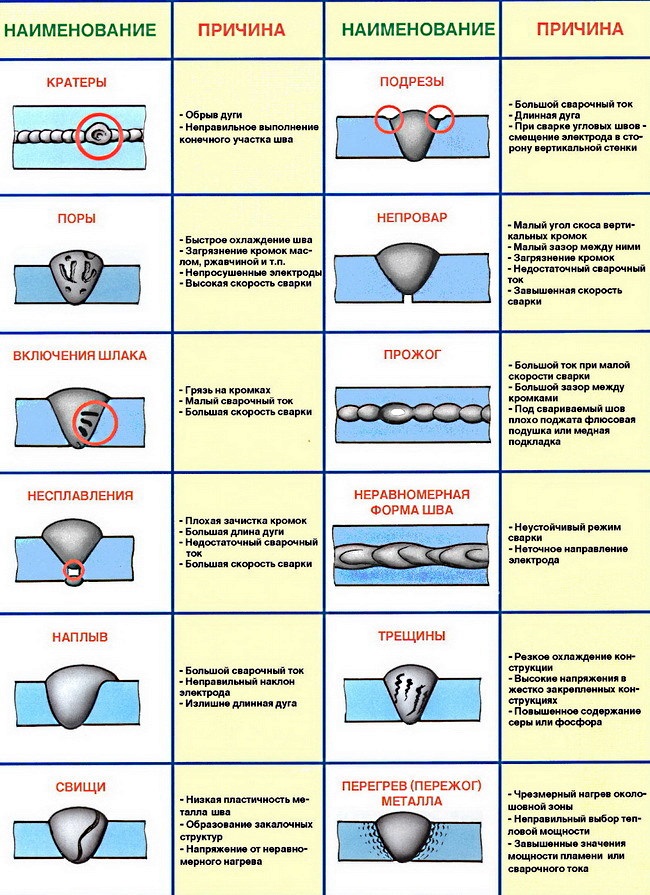
Nedostaci vara
Ti nedostaci tijekom rada mogu dovesti do smanjenja karakteristika čvrstoće metala, smanjenja operativne pouzdanosti i trajnosti cjevovoda, promjena u karakteristikama transporta, nedovoljne preciznosti dimenzija i degradacije izgleda. Glavni uzroci nedostataka su: kršenje tehnologije zavarivanja, korištenje materijala loše kvalitete ili nedovoljna osposobljenost radnika. Viznim pregledom uočljivi su brojni nedostaci u zavarenim spojevima, ali većina njih je skrivena i može ih se otkriti samo posebnim metodama. Drugim riječima, defekti mogu biti unutarnji i površinski (vanjski).
Vrste oštećenja i oštećenja
Moguće je izdvojiti glavne oblike defekata u zavarenim zonama: masovni priljev, podrezivanje, neravnomjerno prodiranje, pukotine i pore (i vanjske i unutarnje), strane uključke.
Nedostaci se mogu podijeliti i zbog njihove pojave. Razlikuju se dvije glavne skupine: defekti uzrokovani metalurškim svojstvima i toplinskim učincima, te nedostaci uzrokovani ljudskim čimbenicima, kršenje uvjeta zavarivanja. Prvi se može pripisati kristalnoj strukturi - pukotinama (hladnim i vrućim) u zavarenom i šavnom dijelu, porama, troski, strukturnim promjenama u metalu. Iz druge skupine ističu se defekti kao što su nenormalizirane dimenzije zavara, neujednačena penetracija, potkopi, opekline, noduli, krateri, neispunjeni metal i neki drugi.
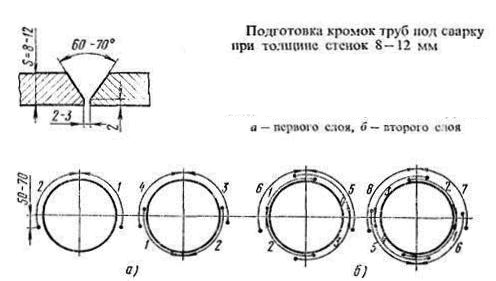
Shema pripreme rubova cijevi za zavarivanje.
Kršenje dimenzija šava može utjecati na pouzdanost cjevovoda, pa ako su takva odstupanja veća od normaliziranih normama, smatraju se nedostacima. Takvi defekti indirektno ukazuju na prisutnost unutarnjih defekata u zavarivanju. Glavni nedostaci ovog tipa su: oštra neravnost širine i visine vara duž njegove duljine, strmi prijelaz iz predzavršene zone u zavarivanje, primjetna hrapavost metala šava, velika sjedala i strugovi.
Cjevovodi: analiza različitih oštećenja
Defekt zavarenog spoja u obliku preljeva pojavljuje se kada talina snažno propušta u hladnu zonu blizu šava. Jedra mogu imati oblik pojedinačnih kapljica i mogu doseći značajnu udaljenost duž zavarenog šava. Uzroci spuštanja:
- višak struje zavarivanja;
- pogrešan nagib;
- pomicanje elektrode tijekom zavarivanja;
- zanemarujući kut cijevi kada su spojeni.
Progib je često popraćen pojavom neujednačenog i lošeg kvaliteta prodiranja metala šava, kao i pojave vanjskih i unutarnjih pukotina.
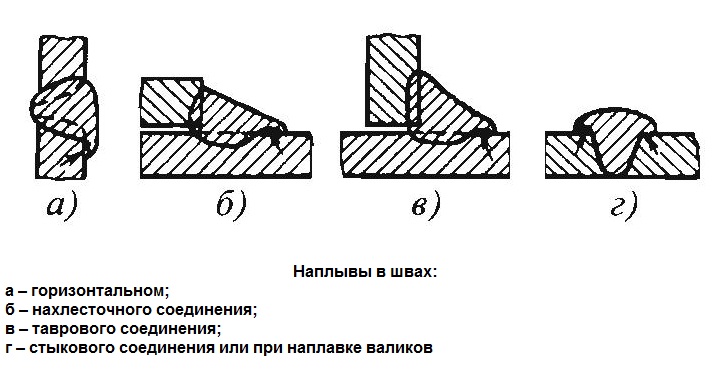
Sheme za formiranje čvorića
Podrezani su utori u metalu koji se pojavljuju na granici sa zavarivanjem. Takav nedostatak smanjuje stvarni presjek šava i dovodi do pojave prekomjernih naprezanja, što može dovesti do njihovog rasta u pukotine s naknadnim uništenjem zavarenog spoja.
Nedostaci u obliku opeklina pojavljuju se kao rupe kroz koje je talina tekla iz varene vrele. Razlog za nastanak takvog defekta može biti niska brzina zavarivanja, precijenjeni razmak između krajeva cijevi kada su zavareni, a jačina struje zavarivanja je premašena. Nedovoljno ili neravnomjerno prodiranje šavova uzrokovano je nedostatkom pouzdanog povezivanja rubova na malim površinama. Takav nedostatak smanjuje stvarni presjek vara i dovodi do zaostalih naprezanja, koje mogu uzrokovati kasnije pucanje i uništavanje metala.
Pukotine se mogu pripisati najopasnijim vrstama defekata. Mogu se pojaviti u bilo kojoj točki zone zavarivanja (uključujući i metalnu površinu) i imati bilo koji smjer (uzdužni i poprečni). Po veličini se dijele na mikropukotine i pukotine. Takav nedostatak je uzrokovan i neodgovarajućim uvjetima kristalizacije taline, kao i viškom koncentracija ugljika, sumpora i fosfora u bazenu za zavarivanje. Pukotine značajno utječu na sve glavne parametre zavarenih spojeva cjevovoda.
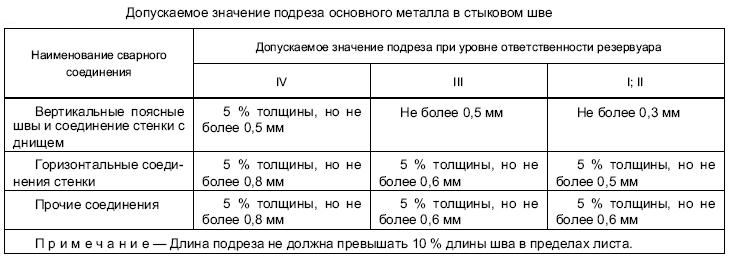
Tablica dopuštenih vrijednosti podrezivanja tijekom zavarivanja.
Strane uključenosti slabe karakteristike čvrstoće. Najopasnija je prisutnost uključaka šljake nastalih zbog nedovoljnog čišćenja troske iz površine zavarenih spojeva nakon zavarivanja. Ove inkluzije znatno ubrzavaju koroziju metala.
Pare plina ili zraka obično se formiraju unutar vara. Oni mogu imati jedan karakter, a mogu nastati u skupinama, pa čak i formirati lance praznina. Pore se mogu taložiti na površini metala, formirajući udubljenja (fistula). Pore značajno smanjuju čvrstoću šavova, a stvaranje lanaca šupljina može uzrokovati smanjenje tlaka cjevovoda.
Kršenja u strukturi metala šava ili gotovo bešavne zone mogu se manifestirati povećanjem koncentracije oksida, mikropora i mikropukotina, krupnih zrna. Toplinski režim u oblikovanju metalne konstrukcije igra ključnu ulogu. Prekomjerno zagrijavanje dovodi do stvaranja velikih zrnaca u strukturi. Kada se metal sagori, mogu se pojaviti zrna s oksidiranim površinama. Sve to dovodi do krhkosti metala.
Opća teorija nerazornih ispitivanja
Pod metodom ispitivanja bez razaranja leži skup metoda koje vam omogućuju da odredite potrebne parametre bez ugrožavanja cjelovitosti zavarenog spoja cjevovoda. Zavareni spojevi moraju se nadzirati u svim fazama pripreme, proizvodnje i pripreme za rad, te povremeno tijekom rada.
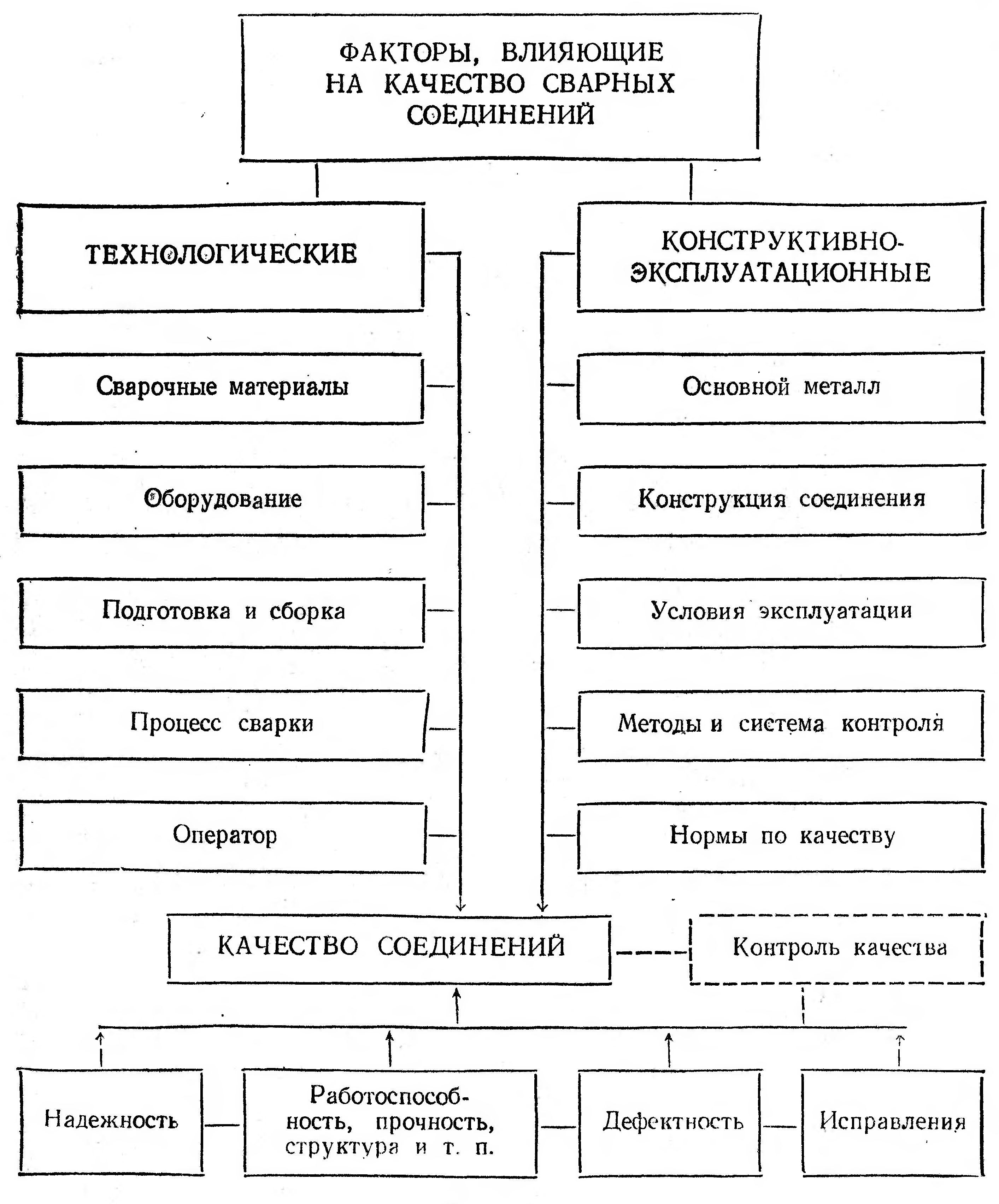
Čimbenici koji utječu na kvalitetu zavarenih spojeva.
Metode nedestruktivne kontrole kombiniraju kontrolu vanjskim pregledom radi otkrivanja vanjskih defekata, proučavaju nepropusnost zavarenih spojeva zavarenih spojeva i metode kontrole za utvrđivanje skrivenih defekata pomoću posebnih uređaja. Ispitivanje bez razaranja dodjeljuje se kao poseban stupanj tehnološkog procesa proizvodnje cijelog cjevovoda.
Državni standardi strogo reguliraju kontrolu zavarenih spojeva cjevovoda. Dakle, GOST 3242-79 definira šest osnovnih vrsta kontrole, a GOST 30242-97 klasificira vrste defekata u zavarenim spojevima cjevovoda. Glavna svrha korištenja posebnih metoda je utvrditi mjesto i veličinu skrivenih defekata, tako da sve tehnike pripadaju skupini za otkrivanje pukotina. Sustav ispitivanja bez razaranja uključuje sljedeće metode: kapilarne, radijacijske, akustične, magnetske, ultrazvučne.
Vanjski vizualni pregled
Prva metoda nerazornog ispitivanja zavarenih spojeva cjevovoda je vanjska vizualna kontrola i mjerenje, koja se provodi kontinuirano u svim fazama proizvodnje i rada cjevovoda. Prije svega, vizualnim pregledom zavarenog spoja cijevi utvrđuje se prisutnost vanjskih defekata, kao što su preljevi, potkopi, krateri pora, opekline, vanjske pukotine i drugo. Prilikom ovog pregleda preporučuje se uporaba povećala s desetostrukim povećanjem.
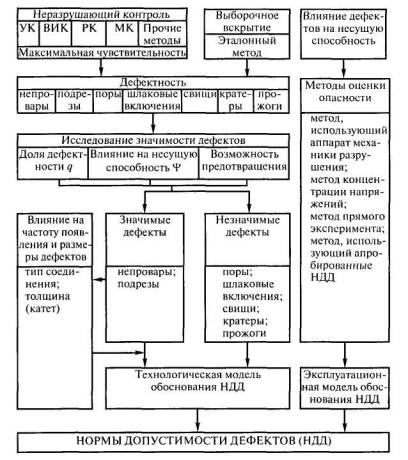
Opća shema dokazivanja normi dopustivosti grešaka.
Sljedeći korak je mjerenje dimenzija zavarenih elemenata i fiksiranje mjesta oštećenja. Prilikom mjerenja utvrđuju se sljedeće dimenzije zavarivanja: širina i visina, veličina konveksnih dijelova i uglovi na granici sa zonom blizu šivanja. Za kontrolu veličina koriste se posebni predlošci. Rezultati mjerenja vara uspoređeni su sa standardiziranim vrijednostima utvrđenim državnim standardima za ove vrste zavarivanja.
Ispitivanje curenja
Spojeni cijevni spojevi moraju biti nepropustni za one tvari (tekućine ili plinove) koje se transportiraju kroz ovaj cjevovod. Kontrola nepropusnosti (nepropusnosti) provodi se nakon sastavljanja cjevovoda. To uključuje sljedeće osnovne metode provjere: kapilarne, kemijske, mjehuriće, kao i usisavanjem i korištenjem uređaja za otkrivanje propuštanja.
Ispitivanje zavarenih spojeva kapilarnom metodom temelji se na svojstvu kerozina za primjenu kapilara za prodiranje kroz unutarnje šupljine (pore, pukotine). Za provjeru nepropusnosti vara nanosi se vodena otopina krede i suši. Sa strane šava nasuprot površine obojene kredom, površina je obilno zalijevana kerozinom. Ako dođe do curenja, na površini od krede pojavit će se tragovi kerozina. Kada se koristi kerozin, bit će moguće odrediti prisutnost unutarnjih defekata veličine manje od 0, 1 mm.
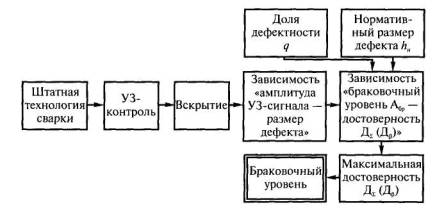
Shema odabira razine odbacivanja s ultrazvučnim ispitivanjem šavova stražnjice.
Kontrola nepropusnosti pomoću amonijaka temelji se na bojanju indikatora nakon dodira s alkalijama. Pokazatelj je otopina fenolftaleina ili žive dušične kiseline, a reagens je amonijak u plinovitom stanju.
Metoda kontrole mjehurića uključuje provjeru tlaka zraka. Komprimirani zrak se pumpa u cijev i nepropusnost zavara provjerava se mjehurićima kada se dio cjevovoda uroni u vodenu kupku. Ispitivanje se može temeljiti na detekciji mjehurića vode pri stvaranju hidrauličkog tlaka unutar cijevi. Prije ispitivanja, površina cijevi se suši, a tijekom ispitivanja osigurava se unutarnji tlak vode koji 1, 5 puta premašuje radni tlak u cjevovodu.
Pri provođenju kontrole zavarenih spojeva kritičnih cjevovoda koristi se kontrola pomoću plinsko-električnog uređaja za propuštanje. Za ispitivanje se koristi plin helij koji ima visoku propusnost. Posebna sonda za otkrivanje curenja otkriva pojavu plina, a elektronska jedinica analizira njezinu količinu i stupanj nepropusnosti vara.
Metoda ugradnje magnetskog defekta
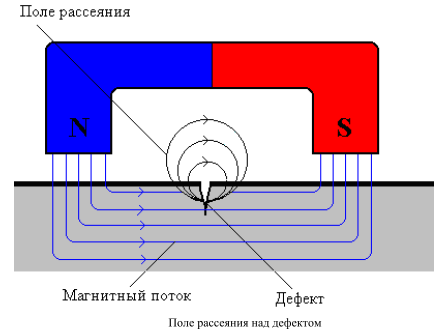
Shema magnetske metode kontrole kvalitete vara.
Nerazorne metode praćenja zavarenih spojeva cjevovoda, uzimajući u obzir magnetna svojstva materijala, omogućuju određivanje lokacije defekata proučavanjem magnetskog raspršenja u neujednačenim strukturama tijekom magnetizacije metala zavarene zone. Dio cijevi je magnetiziran pomoću solenoida smještenog u unutarnju šupljinu ili namotavanjem žice za navijanje preko zavarivanja. Ispitivanje se provodi metodom praha, indukcije ili magnetografske metode, koja se razlikuje metodom mjerenja disperzije magnetskog toka.
Metoda kontrole praha uključuje upotrebu magnetskog praha (željezne piljevine) nanesenog na površinu zavarenog područja. Kada se u prahu stvori magnetsko polje, čestice se orijentiraju i jasno se oblikuje slika magnetskog spektra. Tako možete otkriti pukotine i pore na znatnim dubinama. Za kontrolu pomoću metode indukcije koriste se tragači u kojima se elektromotorna sila stvara pod utjecajem raspršujućeg magnetskog toka. U tom slučaju emitira se zvučni signal ili se pojavi svjetlosni signal. Metoda magnetske kontrole omogućuje snimanje disperzijskog toka na magnetsku traku koja se nalazi na površini zavarenog spoja. Pomoću magnetskog detektora pukotine prisutnost defekata određuje se uspoređivanjem rezultata dobivenih sa standardom.
Metoda zračenja
Metode nedestruktivnog zračenja upravljanja zavarenim spojevima cjevovoda temelje se na svojstvima rendgenskog i gama zračenja. Metali apsorbiraju zračenje različito u prisustvu defekata ili strukturnih promjena, što uzima u obzir ovu metodu provjere. Zavarivanje se provodi kroz zrake pomoću posebnih izvora zračenja. Zrake su fiksirane na poseban film, gdje područja zatamnjenja ukazuju na prisutnost defekata. Položaj i njihove veličine lako se razlikuju. Izvori zračenja su široko korišteni uređaji RUP 150-1 i RUE 120-5-1.
Postupak ispitivanja sličan je rendgenskom pregledu. Sposobnost prodiranja gama zračenja veća je od rendgenske zrake, što povećava mogućnosti zračenja za kontrolu zavarenih spojeva.
Ultrazvučna metoda
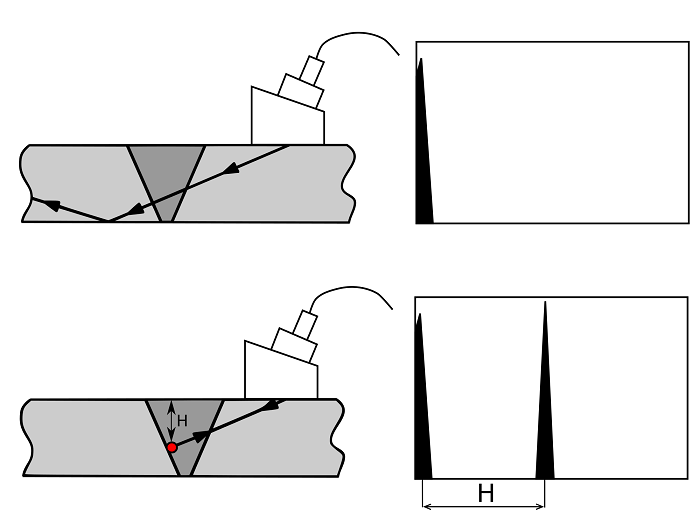
Ultrazvučni pregled zavarenih spojeva.
Nerazorna ultrazvučna metoda kontrole zavarenih spojeva naširoko se koristi za fiksiranje defekata u masi metala. Ova metoda koristi svojstvo ultrazvučnih valova da prodre materijal do znatne dubine i rasprši se na granicama defekata. Izvor vala je piezokristal smješten u posebnu ploču (sonda).
Ultrazvuk se nanosi pod drugačijim kutom od 40 do 73 ° C kako bi se osigurala potpuna slika. Druga ploča uređaja bilježi reflektirane valove. Kao ultrazvučna metoda, najčešće korištena metoda je echo metoda, u kojoj uređaj bilježi izravan odraz pulsa od defekta (echo). Prilikom provjere zavarenih spojeva cjevovoda koriste se ultrazvučni detektori pukotina tipa TUD-320 ili TUD-310. Osim toga, koriste se metode sjenila i zrcalne sjene za ultrazvučnu detekciju pukotina.
Instrumenti i uređaji preporučeni za nerazorna ispitivanja zavarivanja cjevovoda:
- povećalo;
- vernier caliper;
- mikrometar;
- pokazivač dubine;
- uzorci zavara;
- Rendgenski, radijacijski, ultrazvučni i magnetski detektori pukotina;
- pokazatelj propuštanja;
- analizator plina.
Nerazorna analiza zavarenih spojeva cjevovoda važan je element za osiguranje pouzdanosti i sigurnosti. Njegovo ponašanje je regulirano standardima i nužno u proizvodnji i radu cjevovoda.