Bušenje rupa je vrsta obrade metala pomoću rotirajućih alata s metodom rezanja. Ova operacija je podijeljena na duboko bušenje i konvencionalno. U prvoj izvedbi, dubina rupe je veća od 10 cm ili ima veličinu veću od 5 dostupnih promjera (d * 5). Za bušilice ispadaju se utori različitih dubina i promjera (s nekoliko poprečnih presjeka).
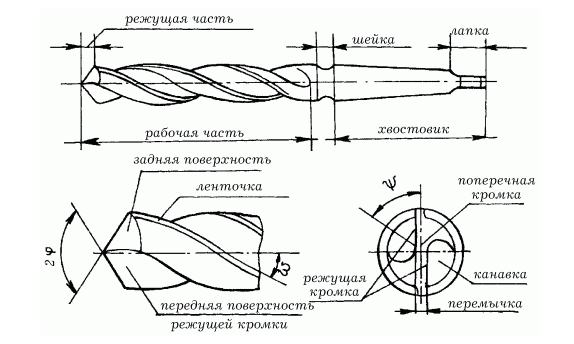
Shema svrdla metala.
Bušenje rupa u metalu moguće je na jedan od sljedećih načina:
- Izvršite rotaciju obratka i istodobno izradite uzdužno nerotirajući alat za bušenje.
- Rotacija obratka se ne provodi, zauzima fiksni položaj.
- Jednokratno kretanje oko svoje osi i mehanizma i pojedinosti.
U praksi su te tehnologije vrlo popularne. Proces formiranja dubokih rupa je vrlo tražen u područjima kao što su proizvodnja cijevi, metalurgija, zrakoplovna i naftna i plinska industrija, proizvodnja ploča izmjenjivača topline i dr. metalne školjke, itd.
Duboko bušenje: klasifikacija
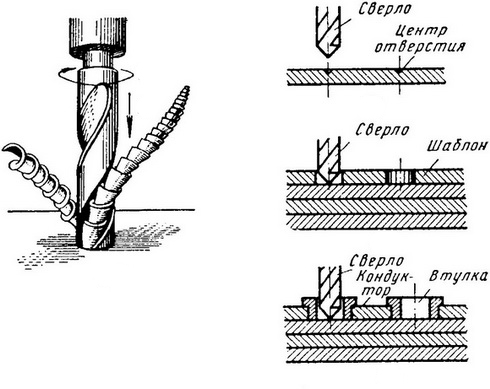
Shema bušenja metala.
- Po vrsti uklanjanja izbušenog sadržaja (čips) emitira: prsten i kontinuirani postupak. U drugoj metodi, izbušeni sadržaj se prikazuje kao čestice čestica, u prvoj metodi, prstenasta ravnina se djelomično uklanja kao štap, a drugi dio se uklanja čipovima.
- Prema metodi rezanja emitira tehnologiju:
Odnoshtangovaya (STS). Ova metoda je optimalna za proizvodnju slijepa u procesu visokih performansi ili masovne proizvodnje. Problem je u tome što morate koristiti uljni prijemnik s raznim opskrbnim crijevima dok istodobno rotirate dio. Ovaj sustav je prepoznat kao najučinkovitiji u formiranju kvalitetnih rupa.
Izbacivanje. Mogućnost dublje obrade s parametrima proizvoda prosječne kvalitete. Strojna obrada se izvodi na strugovima s različitim složenim funkcijama. Sustav uključuje korištenje dodatne mobilne ili instalirane crpne stanice. Ova metoda omogućuje dobivanje rupa promjera 2 do 6 cm dubine do 120 cm, uključujući isprekidane.
Pištolji (cijevne oštrice) buše se s dovodom rashladne tekućine iznutra. Ova opcija pogodna je za mala poduzeća u kojima se predviđaju uvjeti u tehnologiji za izradu rupa malog promjera.
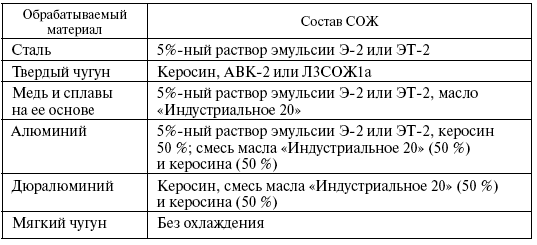
Izbor tablice rashladnog sredstva prilikom bušenja različitih vrsta metala.
Bušilice s jednim rezačem lako su ugrađene u univerzalni princip djelovanja stroja. Rezač je izrađen od tvrdih legura i ima žlijeb u obliku slova V u cijeloj jezgri. Kut prelamanja može doseći 110-1200º. Preporučeni promjer za bušenje je 3, 5-4, 0 cm, duljina - d * 50. Ova metoda ne dopušta operacije postavljanja i razvrstavanja.
Automatsko upravljanje procesom omogućuje vam odabir: dubokog udara s automatskom promjenom jednog ili više radnih parametara (opskrba mazivom, brzina vrtnje itd.).
Značajke procesa dubokog bušenja
Prilikom duboke prerade slijede temeljna načela tehnološkog procesa.
Na početku izvršite odabir brzine vrtnje opreme za bušenje ili maksimalnu moguću brzinu rezanja (bušilice).
Pratite osiguravanje normalnog lomljenja strugotine, potpuno povlačenje sadržaja udubljenja.
Važna nijansa u trenutku uklanjanja otpada je rezač sigurnosnog alata. U ovom dijelu bušilice ne bi trebalo imati oštećenja, kao i oštrice i druge nedostatke. Drugi ključni kriterij za učinkovitu obradu metalnih površina je opskrba tekućinom za hlađenje i podmazivanje prema pravilima.
Budući da su dijelovi bušeni, uz napajanje tekućine za hlađenje i podmazivanje s određenim tlakom i protokom, u sustav se unosi rad crpnih uređaja - pumpi za ulje ili pumpi za pumpanje viskoznih tvari.
Snaga sustava se bira na temelju potrošnje tekućine i potrebne količine tlaka za dobavu maziva.
Opskrba tekućinom je nezamjenjiva točka tehnologije:
- Ispravan izlaz čipa iz radnog područja provodi se putem olovnih kanala.
- Sila trenja između kontaktnih elemenata je smanjena.
- Višak topline nastao tijekom dugog postupka bušenja se uklanja, dok je bušilica očuvana.
- Dodatna obrada iskopa.
Neke poteškoće procesa
S povećanjem dubine, ima više poteškoća s kopanjem.
Dubokim bušenjem koristi se specijalizirani alat koji je tehnički opremljen dodatnim mogućnostima korištenja reznih i drugih vrsta uređaja. To je nužno iz razloga što upotreba standardnih alata ne omogućuje postizanje visokih performansi procesa, a ponekad ga i onemogućuje.